Nadprogramowe szkolenia z bhp poprawiają funkcjonowanie procesów logistycznych
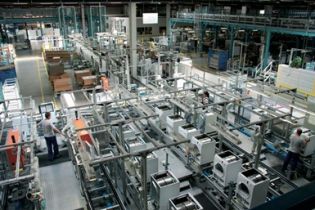
Zapewnienie bezpiecznych warunków pracy w magazynach nie jest proste. Natomiast poziom wypadkowości w branży logistycznej jest wysoki. Są jednak rozwiązania i sposoby, które znacząco poprawiają bezpieczeństwo pracy. Firma BSH Sprzęt Gospodarstwa Domowego zdobywca tytułu „Lidera Bezpiecznej Pracy w Magazynie 2014” dzieli się swoimi pomysłami w zakresie zapewnienia bezpieczeństwa w magazynach.
Wiele wskazuje na to, że branża logistyczna dojrzała do kompleksowego postrzegania zagadnień bezpieczeństwa pracy oraz eksploatacji maszyn i jest gotowa, by nadać tematowi strategiczną rolę. Trudno jednak mówić o rewolucji. W ostatnich latach można było obserwować coraz więcej symptomów rosnącego zainteresowania działaniami prewencyjnymi. Jednym z pionierskich przedsiębiorstw ulokowanych w Polsce, które nadało inwestycjom w bezpieczeństwo priorytetowe znaczenie, jest BSH Sprzęt Gospodarstwa Domowego – zdobywca tytułu „Lidera Bezpiecznej Pracy w Magazynie 2014”.
Działalność BSH w Polsce
BSH Sprzęt Gospodarstwa Domowego to jeden z największych producentów sprzętu gospodarstwa domowego nie tylko w Europie, ale również na świecie. Produkty BSH powstają w 41 zakładach na 4 kontynentach. Cztery spośród fabryk grupy zlokalizowane są w Polsce.
Wszystkie zakłady wyposażone są w najnowocześniejsze rozwiązania technologiczne. Wykorzystuje się tu zaawansowane techniki tłoczenia oraz integrację łańcucha dostaw przez realizację koncepcji shop-in-shop. Jednak z perspektywy bhp szczególnie godnym uwagi aspektem funkcjonowania procesów logistycznych BSH są wdrożone w przedsiębiorstwie systemy zapobiegania kolizjom i wypadkom. – Zapewnienie bezpieczeństwa pracy jest jednym z naszych kluczowych priorytetów – mówi Dariusz Pięta, Kierownik Magazynu Eksportowego w BSH – Dlatego z zainteresowaniem obserwujemy rozwój technologii pozwalających zmniejszyć ryzyko niepożądanych zdarzeń i wdrażamy najciekawsze rozwiązania – dodaje.
Bezpieczne wózki widłowe
Troska firmy BSH Sprzęt Gospodarstwa Domowego o bezpieczeństwo pracy znajduje wyraz w wielu wymiarach funkcjonowania zakładów produkcyjnych i magazynów przedsiębiorstwa. Jednak najbardziej jaskrawym przejawem tej postawy wydaje się lista systemów zaimplementowanych w maszynach intralogisytcznych używanych w BSH.
Na ich flotę składa się kilkadziesiąt elektrycznych czołowych wózków widłowych. Różnią się między sobą osprzętem, wielkością i możliwościami unoszenia. Jednak w większości z nich wdrożono szereg układów zwiększających bezpieczeństwo. – Pojazdy zamawiane przez BSH są najczęściej wyposażane w komplet systemów minimalizujących ryzyko wypadku – mówi Tobiasz Jakubczak, specjalista ds. produktu firmy STILL Polska, zaopatrującej BSH w sprzęt w oparciu o umowę koncernową. – W przeznaczonych dla Firmy wózkach zaimplementowaliśmy między innymi: pełne oświetlenie (w tym reflektor STILL Blue Safety Light), czujniki cofania oraz szereg zautomatyzowanych systemów redukcji zagrożeń: kontrolę szybkości pokonywania zakrętów wraz z wbudowanym limitem maksymalnej prędkości jazdy, monitoring stabilności wózka, system samoczynnej blokady masztu oraz układ automatycznego wyrównania wideł – wymienia Tobiasz Jakubczak.
Bezpieczeństwo? Jasna sprawa.
Jednym z najistotniejszych układów poprawiających bezpieczeństwo procesów intralogistycznych jest oświetlenie poruszających się po zakładzie pojazdów w sposób gwarantujący swobodne wykonanie pracy operatora i widoczność maszyny dla osób trzecich.
Dlatego w wózkach widłowych BSH, prócz standardowych lamp zainstalowano: 3 montowane na dachu robocze reflektory LED – w tym dwa frontalne i jeden tylny, lampę ostrzegawczą oraz system STILL Blue Safety Light, wyświetlający na podłożu 5 m za wózkiem punkt świetlny koloru niebieskiego, ostrzegając osoby trzecie o zbliżającym się wózku. Ma to szczególne znaczenie w strefach z wymogiem stosowania środków ochrony słuchu.
Bezpieczeństwo z automatu
Kolejną grupą wdrożonych w BSH systemów zapobiegania wypadkom są zautomatyzowane układy eliminujące część zagrożeń związanych z pracą operatora. – Układ ATC (ang. Assistance Truck Control) dostosowuje prędkość pojazdu w zależności od kąta skrętu kierownicy, zmniejszając ryzyko utraty stabilności i uszkodzenia towarów na zakrętach – tłumaczy Tobiasz Jakubczak. – Z kolei samoczynna blokada masztu oraz system automatycznego wyrównania wideł zapewniają bezpieczeństwo przy załadunku i rozładunku palet – dodaje.
Optymalne dostosowania urządzeń do zadań
W BSH duży nacisk kładzie się również na dostosowanie urządzeń intralogistycznych do konkretnych zadań – tak, by optymalnie wykorzystać ich mocne strony. W związku z tym, wyeliminowano wózki widłowe z prac bezpośrednio związanych z produkcją. – W BSH do dowozu materiałów na linie montażowe wykorzystano zestawy transportowe złożone z ciągnika STILL CX-T i trolejów dostosowanych do specyfiki używanych półproduktów – mówi Tobiasz Jakubczak, specjalista ds. produktu STILL Polska. – Punkt ciężkości w tym modelu umieszczony jest znacznie niżej niż w wypadku wózków widłowych. Gwarantuje to dobrą stabilność boczną oraz doskonałą przyczepność do podłoża. W otoczeniu, gdzie pracuje wiele osób, nie bez znaczenia jest również nieograniczona kabiną widoczność na wszystkie strony – dodaje ekspert.
Pozytywny wpływ na bezpieczeństwo pracy ma również seryjnie instalowane w typoszeregu STILL CX wyposażenie, takie jak: stopnie z wykładziną antypoślizgową, amortyzowana platforma operatora, stanowisko z bocznymi oparciami pleców oraz wzmocniona osłona przeciwuderzeniowa.
Maszyny to nie wszystko
W kwestii bezpieczeństwa BSH nie ogranicza się jednak do wdrożeń nowych maszyn i urządzeń. – Mamy świadomość, jak istotny w minimalizowaniu liczby wypadków jest czynnik ludzki – mówi Dariusz Pięta, Kierownik Magazynu Eksportowego w BSH. – Dlatego, obok szkoleń uprawniających do prowadzenia maszyn, nasi operatorzy biorą udział w dodatkowych warsztatach – dodaje. Jednym ze szkoleń, które odbyli pracownicy firmy, były zajęcia w ramach Akademii Bezpieczeństwa STILL.
– Na 2 warsztatach przeprowadzonych na rzecz operatorów BSH, omówiliśmy szczegółowo zasady bezpiecznej eksploatacji wszystkich maszyn STILL, z którymi mają styczność w codziennej pracy. Zaprezentowaliśmy również potencjalne konsekwencje nieprzestrzegania tych reguł – mówi Tobiasz Jakubczak, prowadzący Akademię Bezpieczeństwa STILL. – Ze szczególnie entuzjastycznym przyjęciem spotkały się praktyczne warsztaty bezwypadkowej jazdy wózkami widłowymi i konkurs dla najbezpieczniej prowadzącego operatora – dodaje.
– Mamy poczucie, że regularne, „ponadprogramowe” szkolenia z zakresu bezpieczeństwa mają istotne przełożenie na funkcjonowanie procesów logistycznych w naszym przedsiębiorstwie – komentuje Dariusz Pięta z BSH. – Przypominamy dzięki nim o najważniejszych zasadach związanych z prawidłową eksploatacją maszyn i informujemy o technologicznych nowościach. Jeszcze ważniejszym efektem jest jednak pokazanie pracownikom, jak ważne jest dla nas zminimalizowanie liczby kolizji i wykształcenie proaktywnej postawy zapobiegania zagrożeniom. Działania te wymiernie przekładają się na zwiększenie bezpieczeństwa ruchu wewnątrzzakładowego – podsumowuje.
Powiązane treści
Poradnia 48 Portalu BHP
Jeśli masz jakiekolwiek pytania skorzystaj z indywidualnej porady grona naszych wybitnych Ekspertów.
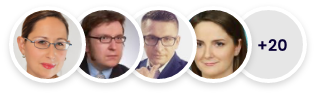
Popularne
Badania kontrolne w trakcie zwolnienia lekarskiego »
Zmiany w medycynie pracy od 2025 r.: Dodatkowe profilaktyczne badania lekarskie pracowników. »
Wskazówki, jak przechowywać butle z gazami? »
Ile minut trwa przerwa w pracy pracownicy w ciąży pracującej przy komputerze? »
Ręczne prace transportowe – zasady bhp »
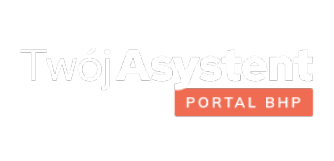
Bądź codziennie na bieżąco ze zmianami w branży BHP, dzięki aplikacji stworzonej przez najlepszych Ekspertów.