PESA Bydgoszcz SA: nowe inwestycje i nakłady na bezpieczeństwo zwracają się
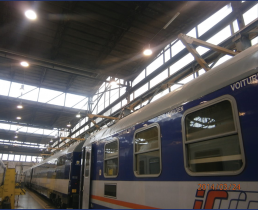
Największy polski producent pojazdów szynowych – PESA Bydgoszcz SA – łączy ponad 160-letnią tradycję i ogromne doświadczenie z nowoczesnością. Firma inwestuje w bezpieczeństwo pracowników, wykorzystuje nowe technologie i opracowuje programy działań. Wszystko to w celu zmniejszenia liczby wypadków przy pracy i zapewnienia bezpieczeństwa pracy. Poznaj rozwiązania jakie wprowadziła PESA Bydgoszcz SA.
Po przeprowadzeniu rzetelnej analizy stanu bezpieczeństwa w firmie wytyczono dwa główne cele, które zostały ujęte w polityce bhp:
- zmniejszenie liczby wypadków przy pracy oraz
- zmniejszenie liczby pracowników pracujących w warunkach przekroczenia NDS,NDN.
Realizacja tych celów spowodowała widoczne zmniejszenie wydatków na ubezpieczenie wypadkowe.
Najwięcej pracowników pracujących w warunkach przekroczeń czynników szkodliwych (pył i substancje chemiczne) – bo aż 115 – zanotowano w 2010 roku. Byli to pracownicy wykonujący prace na stanowiskach spawacza i ślusarza w zakładzie budowy konstrukcji Z-4. Dlatego zdecydowano o wybudowaniu nowej hali z odpowiednim systemem filtrowentylacji oraz wyposażeniu już istniejącej hali w systemy odpylania.
Nowe inwestycje
Wybudowanie nowej hali w 2011 roku z jedną z najbardziej nowoczesnych filtrowentylacji typu Pusch-Pull (koszt wentylacji to 1.320.000zł) i założenie filrtowentylacji typu TCL – Turbo Convection Lift (koszt wentylacji 600.000zł) w hali już istniejącej pozwoliło na wyeliminowanie zagrożenia dla 364 pracowników.
Wybudowanie dwóch nowoczesnych kabin malarskich i kabiny śrutowniczej oraz założenie wentylacji na stanowiskach pracy w pomieszczeniach obróbki tworzyw sztucznych Zakładu PS (500.000zł) spowodowało eliminację zagrożeń pyłami i czynnikami chemicznymi dla kolejnych 26 pracowników.
Zamontowanie instalacji nawiewno-wywiewnej oraz wyposażenie pracownika w maskę z dopływem świeżego powietrza spowodowało wyeliminowanie narażenia pracownika na pyły tworzyw sztucznych w Zakładzie PS (Zakład Tworzyw Sztucznych). Centrala wentylacyjna nawiewna wyposażona jest w filtry powietrza G4, nagrzewnicę wodną, wentylator.
Narzędzia, które pomogły w eliminowaniu zagrożeń to obowiązujące procedury, standardy bhp, wprowadzenie krótkich lekcji i systemu 5S.
Nowe procedury
W firmie wprowadzono procedurę „MONITOROWANIE ŚRODOWISKA PRACY I INFORMOWANIE O ZAGROŻENIACH”. Określa ona sposób eliminacji i minimalizacji zagrożeń przez monitorowanie środowiska pracy (kontrole raportów tygodniowych, raportów miesięcznych, analizy rocznej stanu bhp, zalecenia pokontrolne).
Na podstawie przeprowadzonych codziennych kontroli wszystkie nieprawidłowości są opisywane w zaleceniach pokontrolnych (rodzaj nieprawidłowości, sposób wyeliminowania, termin realizacji).
Następnym etapem są cotygodniowe spotkania szefa produkcji z kierownikami zakładów produkcyjnych. Każdy tydzień jest podsumowaniem tego, co już udało się zmienić, a co jeszcze należy poprawić, kogo pochwalić. Wszystkie te informacje przekazywane są również w raportach miesięcznych i omawiane z prezesem firmy. Informacje o nieprawidłowościach, poprawie i dobrych przykładach znajdują się na tablicach bhp.
W 2013 roku zostało przeprowadzonych 789 kontroli stanu bhp na stanowiskach pracy. Stwierdzono 788 nieprawidłowości i opracowano 209 zaleceń pokontrolnych.
Procedury wewnętrzne postępowania w przypadku wypadków
Celem procedury „POSTĘPOWANIE PODCZAS POWSTANIA WYPADKÓW PRZY PRACY” jest określenie sposobów postępowania zapewniającego skuteczne działania w przypadku zaistnienia wypadku przy pracy oraz przygotowania dokumentacji wypadkowej.
Istotnym elementem w tej procedurze jest to, że przez zakładowych społecznych inspektorów pracy na krzyżu bhp rejestrowane są nie tylko wypadki, które już się zdarzyły, ale również zdarzenia potencjalnie wypadkowe.
Procedura podająca ogólne wytyczne przy ocenie ryzyka zawodowego
W procedurze „IDENTYFIKACJA ZAGROŻEŃ I OCENA RYZYKA ZAWODOWEGO” podano ogólne wytyczne do postępowania przy przeprowadzaniu identyfikacji zagrożeń i oszacowaniu ryzyka zawodowego. W zespołach, które identyfikują zagrożenia oraz szacują ryzyko zawodowe (obowiązująca metoda RISC-SCORE, a dla czynników mierzalnych metoda PN) obowiązkowo uczestniczą pracownicy.
Największym zagrożeniem, które wymagało podjęcia szybkich działań eliminujących, były prace na wysokości na dachach nowo budowanych i naprawianych pojazdów. Pracownicy wykonujący prace nie mieli odpowiednich systemów zabezpieczających, dlatego stanowiska pracy, na których istnieje zagrożenia upadku z wysokości, zostały wyposażone w odpowiednie systemy zabezpieczeń:
- linowych typu DUO, PROLINER w Zakładzie Z-3, Zakładzie Z-2, Malarni PML,
- systemy rusztowań na stanowisku budowy tramwaju w zakładzie Z-3, Zakładzie Z-2, Malarnia PML,
- w pomosty i katedry w Zakładzie Z-4.
Kolejnym zagrożeniem, które należało zminimalizować, to prace związane z transportem zarówno ręcznym, jak i mechanicznym (prace z użyciem zawiesi, suwnic, żurawi, przetaczanie pojazdów szynowych, poruszanie się pojazdów kołowych, poruszanie się pieszych).
Pracownicy stosowali uszkodzone zawiesia, często pozostawiali je porozrzucane na stanowisku pracy (30% ze wszystkich zdarzeń wypadkowych na przestrzeni kilkunastu lat od 2001 r. stanowiły wypadki z użyciem nieprawidłowego zawiesia).
Z prawidłowego użytkowania zawiesi przeszkolonych zostało 250 pracowników. W każdym zakładzie wyznaczono miejsce ich składowania na odpowiednich stojakach zawiesi. Ważne jest to, że pracownicy sami wyznaczyli miejsce składowania zawiesi oraz w zależności od rodzaju zawiesia zaproponowali wzory stojaków do ich składowania i sami je wykonali w poszczególnych zakładach.
Pracownicy komórki bhp (specjalista ds. bhp i starszy inspektor ds. bhp) uczestniczyli w szkoleniu z zakresu bezpiecznej eksploatacji zawiesi organizowanym przez UDT. Została opracowana instrukcja bezpiecznej eksploatacji zawiesi, w której zostały m.in. podane przykłady zużycia zawiesi kwalifikujące się do wycofania z eksploatacji.
Stosowanie i używanie płóz
Stosowanie i używanie płóz stanowiących zabezpieczenie przed staczaniem się pojazdów szynowych było również niewłaściwe i spowodowało dwa poważne ze względu na uraz zdarzenia wypadkowe oraz zdarzenia potencjalnie wypadkowe.
Wdrożono działania korygujące. Opracowano instrukcję bezpieczeństwa pracy przy posługiwaniu się płozami. Ponadto 103 pracowników zostało przeszkolonych przez instruktora ruchu kolejowego z zakresu eksploatacji płóz.
System zarządzania produkcją „LEAN MANUFACTURING”
Istotnym i bardzo znaczącym elementem w eliminowaniu zagrożeń było wprowadzenie w firmie narzędzia Systemu Zarządzania Produkcją „Lean Manufacturing”, Systemu 5S.
System 5S to metoda organizacji i uporządkowania stanowiska pracy, służąca:
- poprawie bezpieczeństwa,
- wykorzystaniu przestrzeni,
- wyeliminowaniu tzw. zbędnego szukania,
- posiadania nadmiernych stanów narzędzi i materiałów.
Metoda ta wykorzystuje zarządzanie wzrokowe, poprawia ergonomię, zmniejsza liczbę zagrożeń występujących na stanowisku pracy.
Elżbieta Muszyńska
kierownik Działu Bezpieczeństwa i Higieny Pracy PESA Bydgoszcz SA
Słowa kluczowe:
bezpieczeństwo i higiena pracy (bhp)bezpieczeństwo pracypoprawa stanu bhpprocedury bezpieczeństwaPowiązane treści
Poradnia 48 Portalu BHP
Jeśli masz jakiekolwiek pytania skorzystaj z indywidualnej porady grona naszych wybitnych Ekspertów.
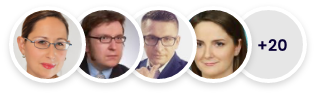
Popularne
Badania kontrolne w trakcie zwolnienia lekarskiego »
Zmiany w medycynie pracy od 2025 r.: Dodatkowe profilaktyczne badania lekarskie pracowników. »
Wskazówki, jak przechowywać butle z gazami? »
Ile minut trwa przerwa w pracy pracownicy w ciąży pracującej przy komputerze? »
Ręczne prace transportowe – zasady bhp »
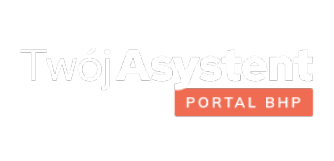
Bądź codziennie na bieżąco ze zmianami w branży BHP, dzięki aplikacji stworzonej przez najlepszych Ekspertów.